Design for Manufacturing
Design for Manufacturing (DFM) is a systematic approach that focuses on designing a product in a manner that optimizes its manufacturability. The goal of DFM is to enhance the efficiency of the manufacturing process by considering various factors during the design phase, such as material selection, component placement, ease of assembly, and overall production processes. This proactive approach aims to streamline manufacturing operations, reduce production costs, and improve the overall quality and reliability of the final product.
Initiating the DFM process begins with collaborative design reviews involving cross-functional teams. This ensures that design considerations are seamlessly integrated from the conceptual stage, fostering a holistic approach to manufacturing efficiency.
Our experts meticulously analyze and optimize material selections to strike the right balance between functionality, durability, and cost-effectiveness.
We focus on simplifying assembly processes without sacrificing the complexity of the final product. This involves strategic component placement, standardized interfaces, and modular design elements contributing to ease of assembly on the production line.
Prototyping is a pivotal step in our DFM approach. We create prototypes to validate the manufacturability of the design, identifying and addressing potential challenges early in the process. This proactive validation ensures a smooth transition from design to production.
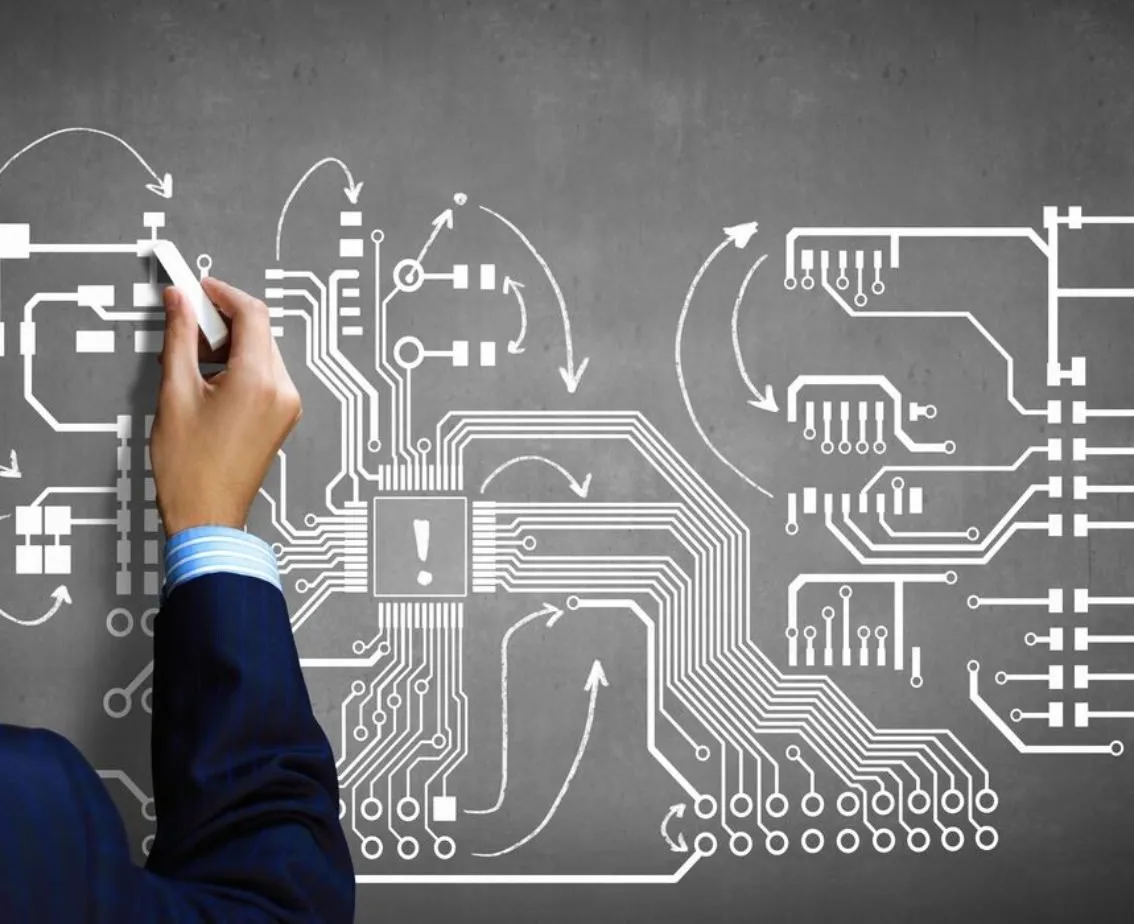
Indic Electronics boasts a proven track record of successfully implementing DFM principles. Our history of delivering products with optimized manufacturing processes showcases our expertise in this critical aspect of product development.
Our DFM services are designed to reduce production costs without compromising on product quality. We identify cost-effective solutions without sacrificing the integrity of the design, ensuring a competitive edge in the market.
DFM is an evolving process, and we are committed to continuous improvement. Staying abreast of the latest manufacturing technologies ensures that your product benefits from the most efficient and cost-effective manufacturing processes.
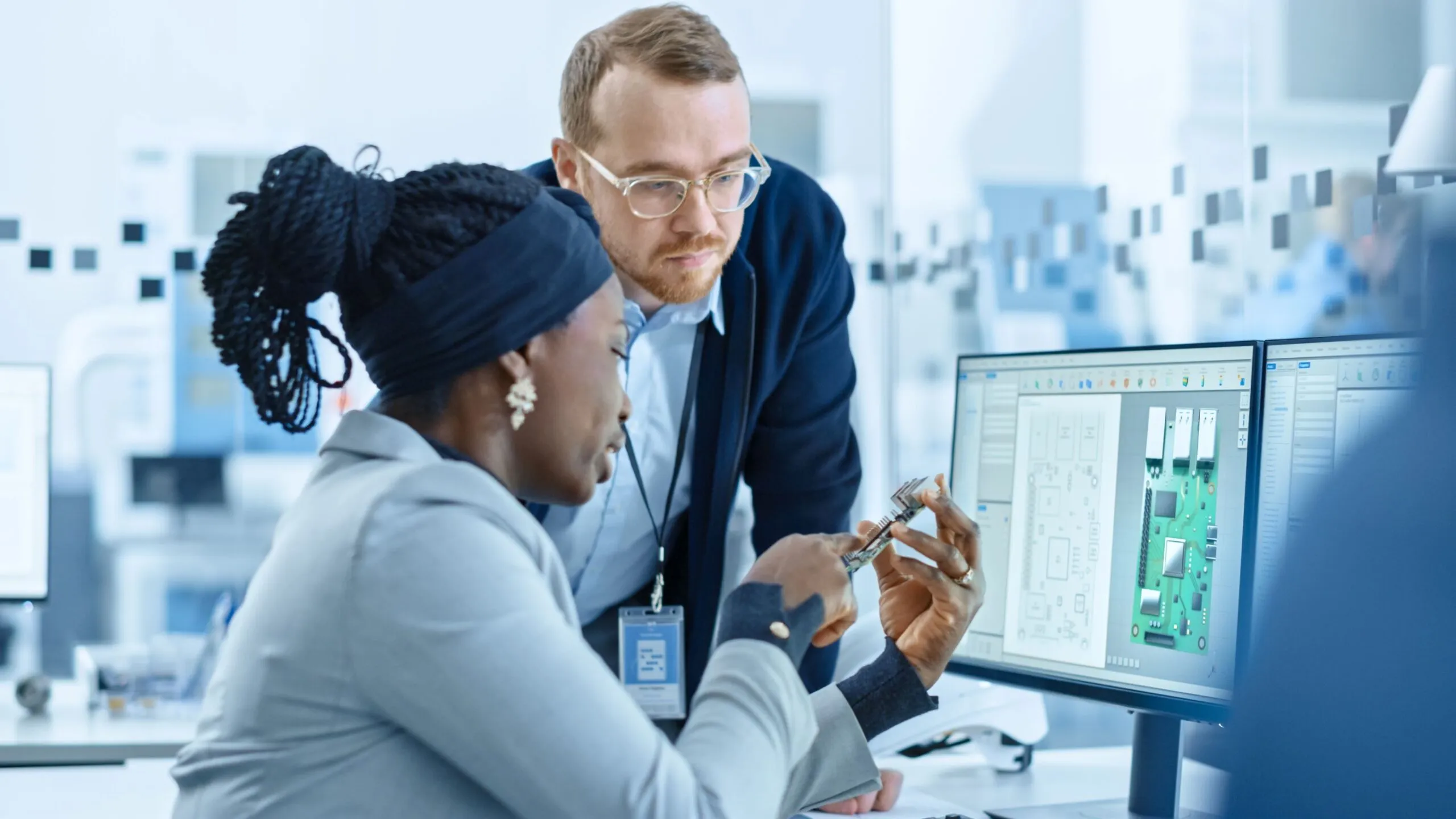
Our Capabilities
With our expertise, we determine the right manufacturing processes for the PCB. The considerations at this stage include:
- Dimensions
- Size
- Material required
- Tolerance
- Steps required in assembly, and more
- Functionality
Product Design
This part of the design for manufacturability exercise involves rectifying any design issues prior to manufacturing. All design modifications are made keeping into account fundamental design principles.
Product Material
This involves determining what materials are necessary for production. This step involves checking for strength, texture and thermal properties of the material.
Operating Environment
We undertake a thorough evaluation of the exact environment under which the product needs to operate. The impact of the environment on the material and shape of the product, for example, is determined at this stage.
Testing
The final stage is to determine whether the design and the materials used conform to the regulatory rules and standards set for the PCB.
The importance of design for manufacturing lies in its potential to significantly reduce production costs, improve product quality, speed up time to market, and ensure product reliability. DFM facilitates efficient manufacturing processes and enhances product lifecycle management.
DFA (Design for Assembly) focuses on designing products for ease and efficiency of assembly, while DFM (Design for Manufacturing) aims at designing products for cost-effective and straightforward manufacturing. Both are critical for reducing production costs and improving product quality.
Manufacturability Assembly efficiency Material choice Compliance with standards
Minimize part count Standardize components Ease assembly Use modular designs Select materials wisely