INDIC Pioneers Fast 4-Day Assembly Cycle of EV Chargers
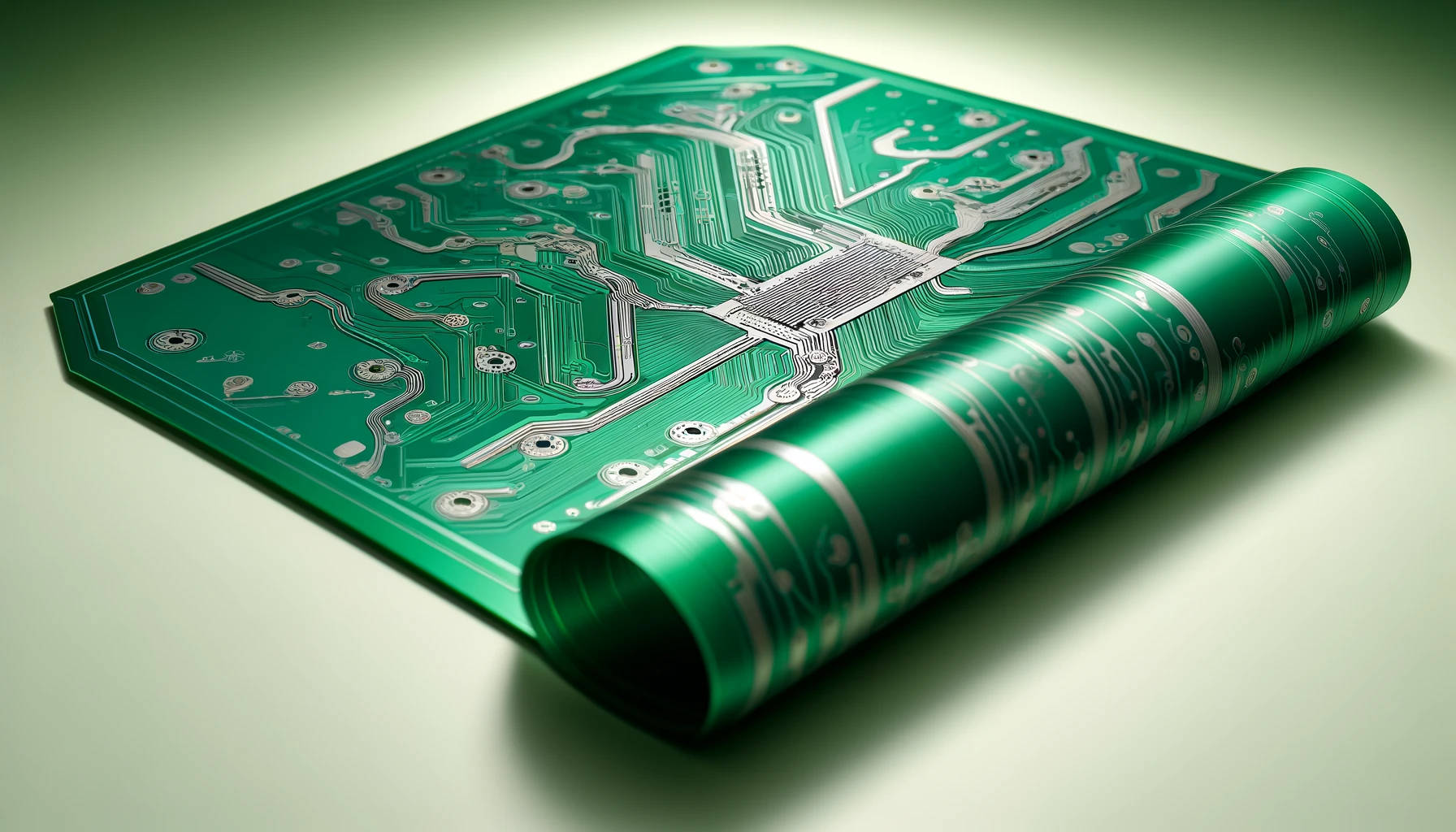
5
In the rapidly evolving electric vehicle (EV) industry, the development and certification of charger assemblies play a crucial role in maintaining safety standards and ensuring compatibility with the charging infrastructure. A leading automobile player in the EV market aimed to localize the production of a 3-wheeler charger assembly for their electric vehicles, transitioning from reliance on international suppliers to domestic production. This case study explores the challenges and innovative solutions involved in obtaining the Automotive Research Association of India (ARAI) certification for this critical component.
The Challenge
The project faced a significant hurdle: the existing process for assembling the charger took two weeks from raw materials to finished goods. However, to apply for ARAI certification—a crucial step in validating the charger's safety and performance—the company needed at least 10 units within a mere five days. This tight timeline presented a formidable challenge, given the intricate process of assembling Power Factor Correction (PFC) boards, control boards, power boards, and the final box build assembly.
The Innovative Solution
In response to this challenge, Indic, the manufacturer tasked with producing the charger assemblies, devised a revised plan to expedite production without compromising quality. Key innovations included:
- Parallel Processing: By simultaneously working on the PFC board and loading SMT components on both the top and bottom, and prioritizing the assembly of the power board due to its critical nature, Indic was able to significantly cutdown production time.
- Box Build Assembly Prioritization: Starting the box build integration before the boards were ready allowed the assembly of the external housing and the potting process to be completed in parallel with board production.
- Efficient Integration: Integrating input and output power supply cables into the box build solution further streamlined the process, ensuring all components were assembled efficiently and effectively.
Impact
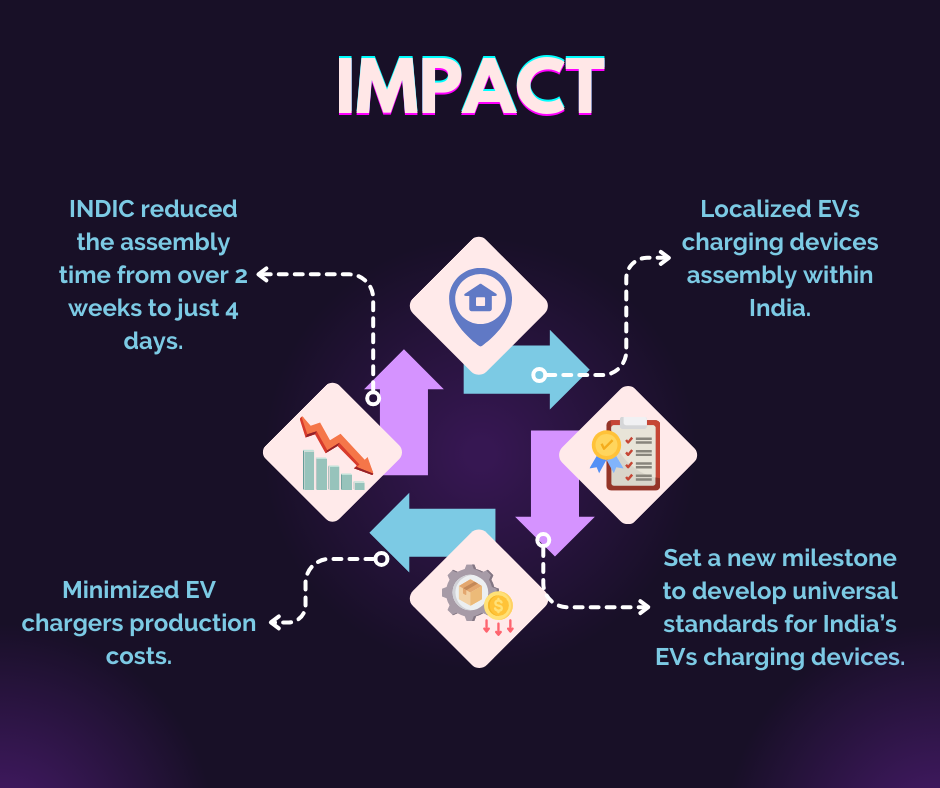
INDIC successfully developed a high-functionality model that streamlined the assembly and testing of complete EV chargers to just four days, with deliveries to the EV company on the fifth day. This significantly reduced the assembly cycle time, previously taking at least two weeks to manufacture a 3 kW EV charger.
Leveraging its robust electronics components production and assembly infrastructure, built over many years of operations, INDIC achieved full localization of its EV charger manufacturing. All device parts and assembly processes handled entirely within INDIC’s local facilities, allowing for a significant decrease in production costs by utilizing local component supplies and manufacturing capabilities.
Furthermore, the lack of unified standards among electric vehicle manufacturers in India and globally has been a significant barrier to market development. This initiative by INDIC represents a crucial step forward, marking a new milestone in the collective effort to establish universal standards in the field.
About Indic and EV Charger Assembly in India
Indic's success in this project marks a significant milestone in the localization of EV charger assembly production in India. Previously, the market relied heavily on imports from China, but geopolitical tensions and the push for self-reliance have spurred efforts to develop domestic capabilities. Indic's achievement in producing and certifying charger assemblies domestically showcases the potential for India to become a leader in EV infrastructure development.
Conclusion
This case study highlights the innovative approaches and strategic planning necessary to overcome manufacturing challenges in the fast-paced EV industry. Indic's ability to meet tight deadlines for ARAI certification not only supported the EV player’s goals for localizing production but also set new standards for efficiency and cost-effectiveness in charger assembly manufacturing. As the EV market continues to grow, such achievements will be crucial in establishing robust, local supply chains that can support the demand for sustainable transportation solutions.